What You Need to Know About Thin-Film Coating
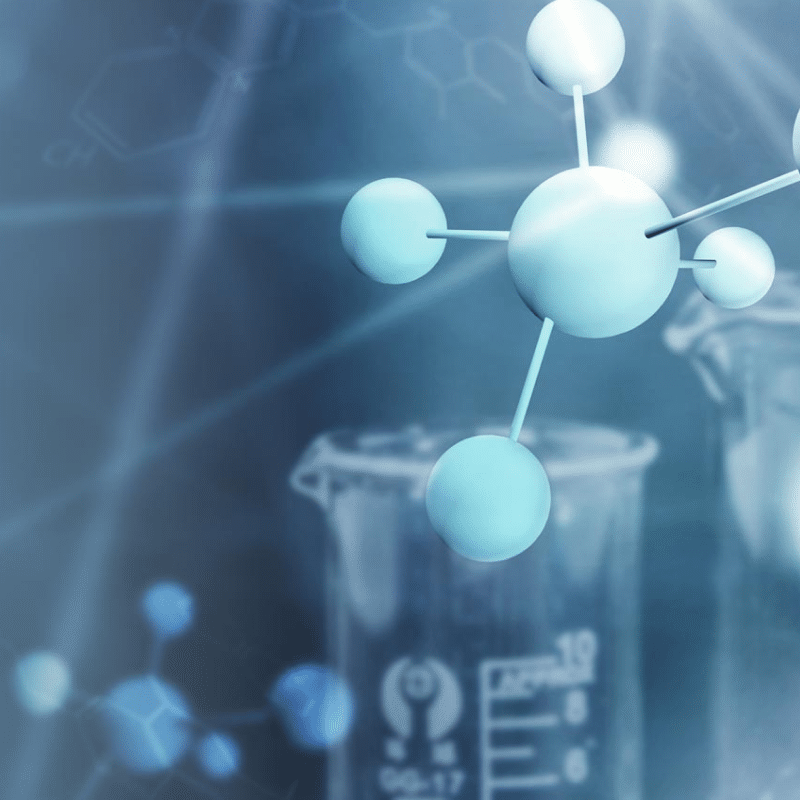
What are Physical and Chemical Vapor Deposition (PVD and CVD)?
PVD thin-film coating is a process in which a solid material, often a metal, is vaporized in a vacuum and deposited, atom by atom, onto the surface of a part. The material may be combined with nitrogen, oxygen, or a carbon-containing gas to form compound materials. This process forms a thin, bonded, metal or metal-ceramic layer on your part or product’s surface that greatly improves its appearance, durability, and performance. The deposition process is adjusted to change the color, durability, or other characteristics of a coating.
PECVD (plasma-enhanced chemical vapor deposition) vacuum coating is a similar process in which the atoms in a gas are energized and deposited on a surface. Diamond-like carbon (DLC) is an example of a thin-film coating deposited using a PECVD process.
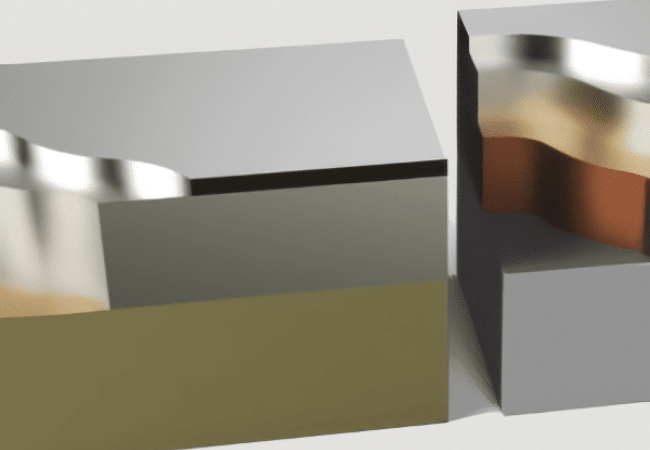
What is PVD coating?
How does vacuum deposition work? What are the benefits? Get the answers in our FAQ.
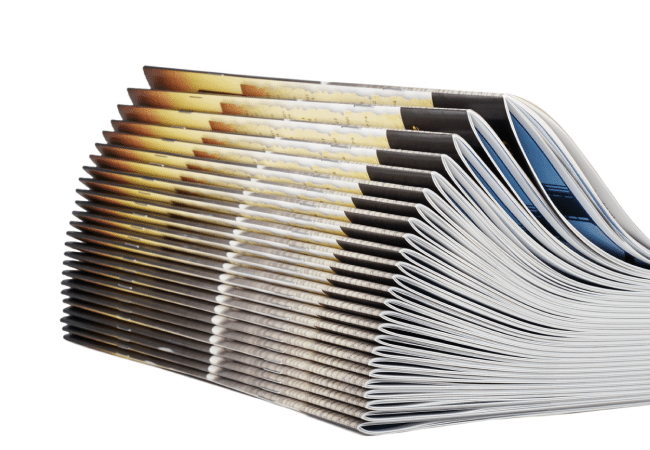
Download system brochure
Read & download detailed VaporTech systems information and specifications.
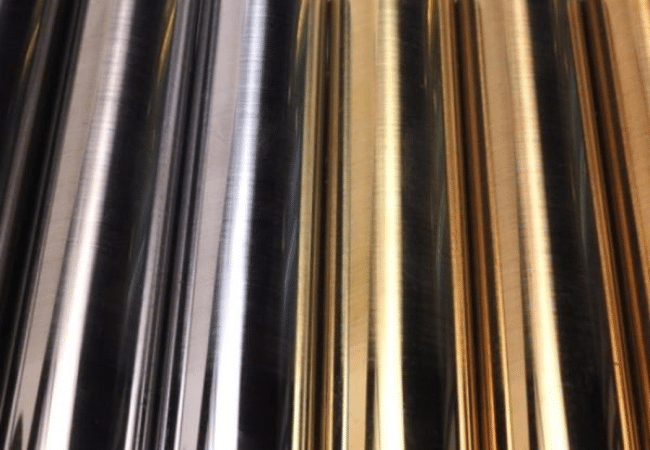
VaporTech PVD & DLC coatings
Discover new decorative and performance thin-film coating options that improve your parts and products.
Download VaporTech PVD resources:
Brochures, charts, case studies, articles, and more.
Easily integrate deposition systems into your existing processes
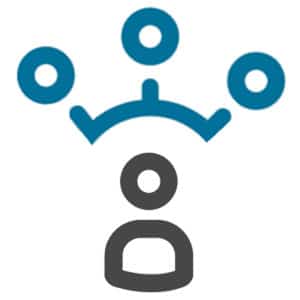
Collaboration:
Our scientists work closely with you to create coatings optimized for your specifications.
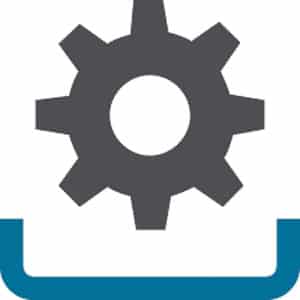
Installation/training:
We provide onsite installation and train your staff.
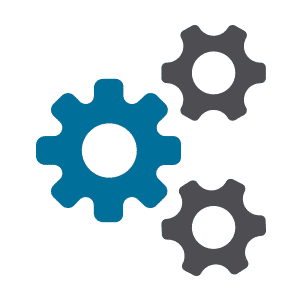
Support:
To keep your equipment running for years to come, we provide maintenance and support.
How do VaporTech systems work?
PVD and DLC PECVD coatings are deposited using a thin-film deposition system. VaporTech systems consist of a vacuum chamber, pumping system, and power supplies that drive the deposition process. A batch of parts are loaded into the vacuum chamber and coated in a fully automated process. Once a thin-film coating is applied, parts may go directly to assembly or packaging. Systems are available in multiple sizes to coat small or large volumes of different size parts (up to 1.2 meters or 48 inches). Both metal and plastic parts can be coated using unique VaporTech low-temperature processes.